In the context of the whole economy in the world more volatile, businesses are facing challenges to optimal lean system management to save cost, achieve high performance in all activities. This article Lac Viet Computing will provide comprehensive perspective about the system operation management business number streamlined and performance.
1. Learn about operation operation management what is?
Operation management business is the implementation, operation control, production, business of business. Includes planning, organization, process setup, deployment, and monitoring, to ensure that resources are used in a reasonable manner.
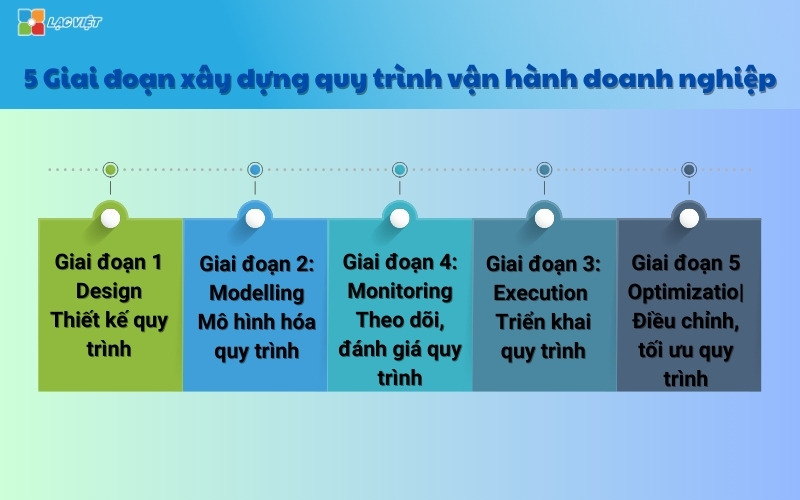
To build the management system operated business streamlined performance should implement processes 5 following stages:
- Stage 1. Design – process design: choosing design the processes necessary based on the objectives, business requirements and include the specific steps required resources, the time taken.
- Stage 2. Modelling – modeling process: construction of the pattern visually show the process steps will be deployed in practice. this step helps to clearly identify the weaknesses, the potential and opportunities to improve the process before implementation.
- Stage 3. Execution – deployment process: The process is being implemented with the participation of the personnel department related, requiring coordination between the department to ensure the work according to plan on the process has been designed.
- Stage 4. Monitoring – monitoring, evaluation process to make sure that every works out according to plan. The criteria of quality, progress and effectiveness to be monitored. Data from the follow-up process will be used to evaluate the performance of the process, timely detection of deviations or points of congestion.
- Stage 5. Optimization – tuning, optimization is done based on the results in stage 4 to optimize the process. This stage focuses on eliminating the knot clog operation, improved step less effective.
>>> Vietnam has implemented a detailed article on the process of building operations, can see more detail AT THIS
2. Important elements in the management system operated business
2.1 Standardized business processes
Standardized processes is related to the setting of the operation process a clear – consistency to ensure that all employees understand and follow the same standard.
The goal of normalization is to ensure that the process of work is streamlined to save the cost, but bring the highest performance with the steps as follows:
- Define goals: Lay out specific goals for the standardization process, such as to optimize costs, improve performance and minimize risk.
- Mapping process: Create diagrams describe current procedures to identify the points that need improvement.
- Join from the related parts: Ensure that all relevant parts are involved and contribute ideas to the standardization process.
- Standardized or build new processes: adjust existing processes or set up new processes to optimize efficiency.
- Construction documentation: Create a document with detailed instructions on new processes to ensure that employees perform properly.
- Staff training: staff Training on the standardized processes to ensure they understand and effectively implemented.
- Check and adjust: monitor, evaluate, perform the adjustment process after deployment to ensure suitability.
2.2 quality Management product (6 – Sigma)
Method quality management (6 Sigma) is used to measure management performance, in-process quality management and operation of production. By finding out the cause and handle them right from the early stages, 6-Sigma helps to increase accuracy, efficiency of the process.
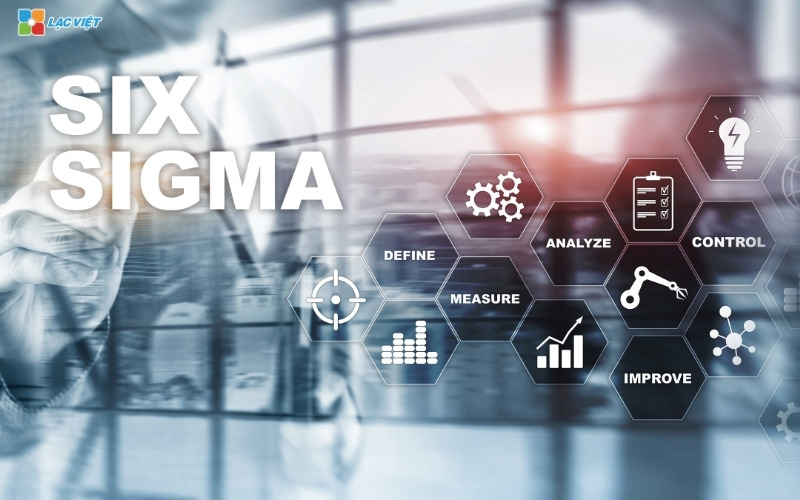
Managed product quality to minimize the limitations in the production, directed to improving the entire production process, sets the standard end products meet the requirements of customers. Use 6 Sigma, businesses can optimize processes, save costs and improve satisfaction of customers.
The main steps in the process, 6-Sigma, including:
- Define the problem: Identify and clearly defined problem to be solved.
- Measurement: collect data to measure the current state of the process.
- Analysis: analyze data to determine root causes of problems.
- Improvements: develop and deploy solutions to eliminate the root causes.
- Control: Monitoring process after improvement to ensure that the improvements are maintained.
2.3 lean Manufacturing
Lean manufacturing (Lean Manufacturing) is a system of tools and methods, production management aims to eliminate waste, the irrational in the process of operational management of production. The main objective is to reduce production costs, shorten operation time, increase output for the business.
Waste in production can exist in many forms, including the waiting time process is not necessary, overproduction, transportation, inefficient, excess inventory,... By removing the waste this business can optimize production processes, improve the flow of products from the start to completion, ensure each step in the process will contribute to increased value for customers.
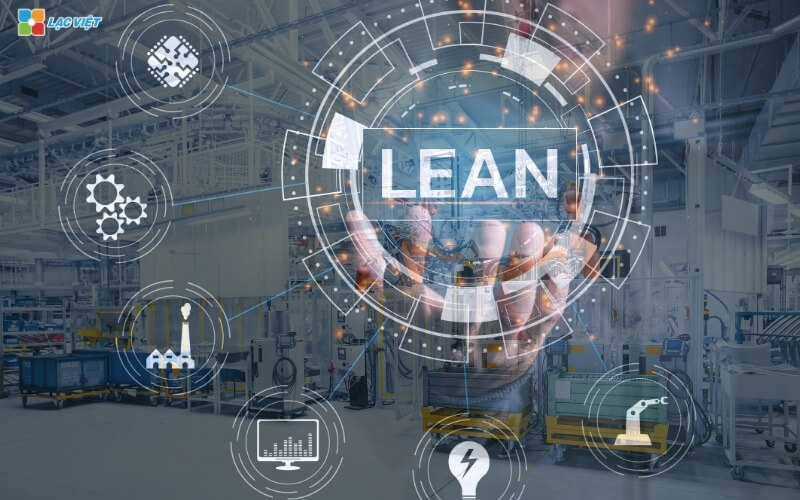
Lean manufacturing focuses on three main principles:
- Eliminate waste: identify and eliminate activities that do not create value in the production process.
- Continuous improvement: Always looking for opportunities to improve processes and enhance performance.
- Optimized flow: Ensures that the products move through the manufacturing process in a continuous manner.
3. Building management system operator of streamlined performance
To build the system of operational management of streamlined performance, applying technology is indispensable. Software, LV-DX Dynamic Workflow is an optimal tool to help businesses digitize the entire operation process, thereby improving operational efficiency.
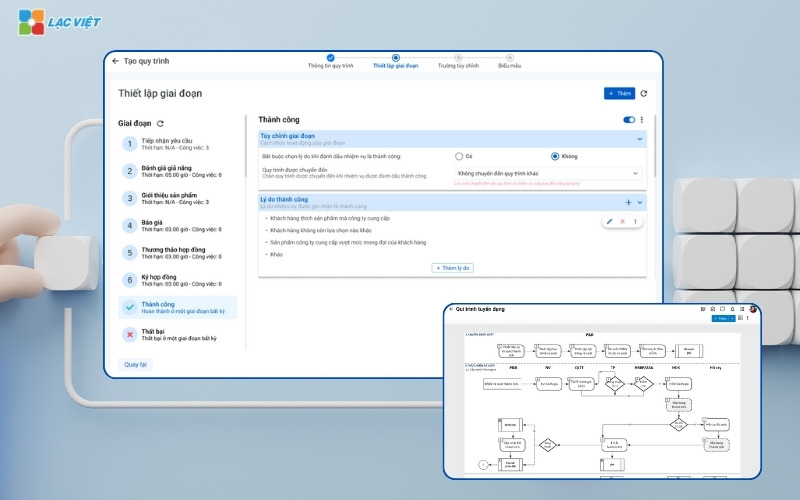
With LV-DX Dynamic Workflow, businesses can:
- The number of turns the whole operation process, created a management system, homogeneous, making all activities that occur smoothly.
- Operating throughout with feature register number approved integrated chatbot WHO helps leaders checking data, approved quickly anytime, anywhere and on any device.
- Evaluate the effectiveness of the operating system with comprehensive reporting system visual tracking.
- Quickly detect the point of obstruction to improvements in operations. Case occur the points of congestion, the system ensures that all knots problems are discovered and solved timely business support, maintain peak performance.
LV-DX Dynamic Workflow do to simplify the conversion process of?
Provides system management – standardized process of comprehensive
- Free build standardized processes for each business, based on the requirements given and the structure departments, by operation of business when BUYING a software package process of Vietnam.
- The system allows the storage of the entire workflow on a single platform, data is synchronized, unified, easy synthesis and analysis.
- Provide inventory process standard reference model for construction business.
Provides system management – standardized process of comprehensive
Every activity, work performance managed, tracked live realtime (real time) on the process
- LV-DX Dynamic Workflow integrated management software, job LV-DX Task to help work directly on the process.
- Automatic transfer of tasks to employees, the next division at the end of the 1 stage in the process.
- Track progress of implementation of the process, the work performance of each employee in real time.
- Warning system work smart, auto send notification to employees involved when a process is established, the transfer task alerts, overdue done, ...
Every activity, work performance managed, tracked live realtime (real time) on the process
Application AI to help optimize performance operating procedures business
- Integrated LV-DX eSign help job approval, signing a number of fast everything, everywhere on the process of. Leadership does not need to come to the company to make up for document browsing, now all operations can be performed remotely at all times with LV-DX Dynamic Workflow.
- Integrated chatbot WHO Lost Vietnam to help the leader out of control, the accurate data on the file browser to help the number quickly, avoid reporting anything complicated, optimal time is work, leaders have more time to build your business strategy, long-term performance improvements for the organization.
Apply the method of administration advanced integrated modern technology into the system operation management to help businesses optimize performance, promote sustainable development. A system administrator commissioning of the effect will be solved the knot, point conception, as well as help business ready to face the volatility of the market.
CONTACT INFORMATION:
- Lac Viet Computing Corporation
- Hotline: 0901 555 063 | (+84.28) 3842 3333
- Email: info@lacviet.vn – Website: https://lacviet.vn
- Headquarters: 23 Nguyen Thi Huynh, P. 8, Q. Phu Nhuan, Ho Chi Minh city