Start is a management solution, improved the quality of the manufacturing process, however the current Six Sigma has been implemented and widely applicable for other fields such as finance, health, business,...However, not everyone can master the entire knowledge of this method to apply and bring the best results.
So What is Six Sigma? In the article below, let's find out details about this term, as well as how it applies to operating procedures business, okay.
1. Learn what is Six Sigma?
Six Sigma (6σ or 6 Sigma) is developed by Motorola in the 1980s. This is a system of quality management focused on reducing errors, defects in the production process and services. The ultimate goal of Six Sigma is to achieve the level of perfection, almost absolute, with only 3.4 defects per million opportunities.
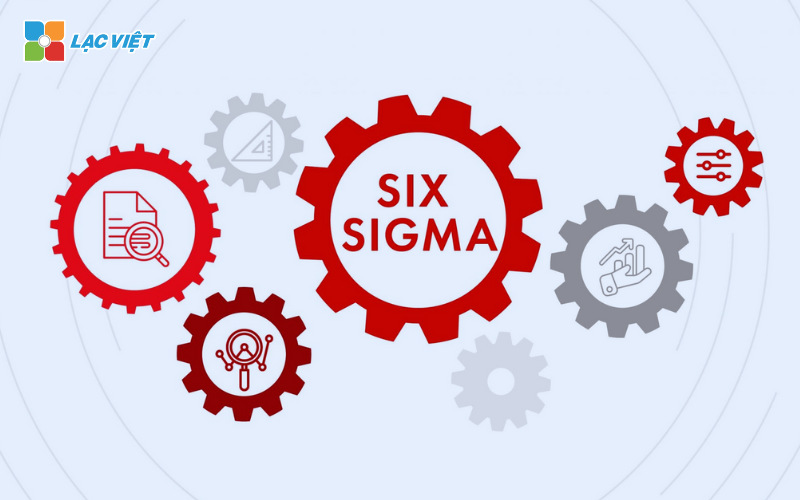
6 Sigma in quality management plays an important role in improving the operational efficiency of the business as follows:
- Improve the quality of products/services: Reduce errors and defects, ensure products/services of a high standard.
- Increase productivity: By optimizing the process, 6 Sigma to eliminate waste, reduce time to complete the work, thereby increasing labor productivity.
- Reduce costs: Reduce production costs due to reduce errors, waste products and waste.
- Increased satisfaction of customers: When products/services are of high quality, customers will be more satisfied, have the ability to go back over.
- Improve business image: The application of Six Sigma shows the commitment of business with respect to quality, thereby improving the image of the business in the market.
Example of 6 Sigma success, not to mention the case study Samsung. By adopting radical to this method at all stages of production, business until the management, Samsung has from a brand with products more bugs become a big market leading global smartphone owns the phone line such as Galaxy S7, S7 edge and J7 Prime.
2. 5 principles apply methods of Six Sigma in quality management
After you have understood What is Six Sigma and would like to successfully apply this approach to quality management, business need to master 5 basic principles the following:
- Customer-centric: All improvement activities are oriented towards meeting the expectations of customers. By clearly identifying the needs, expectations of customers, businesses can build cost-effective processes, minimize errors, to bring maximum satisfaction.
- Admin active: Businesses need to proactively identify the potential risks and implement preventive measures to prevent problems arising. This helps reduce the cost, enhance the stability of the process.
- Theme data: 6 Sigma in quality management is a method based on the data, so the decision was made to rely on the analysis of statistical data. The collection, analysis as well as to interpret the data correctly is very important. Because it affects the identification of root causes of problems and evaluate the effectiveness of improvement measures.
- Collaboration is not limited to: To achieve success with Sigma 6, the cooperation between the department, rank in the organization is very necessary. Every individual has an important role in process improvement. Creating a work environment that is open and encouraged to share ideas, support each other is a prerequisite.
- Towards the perfection, but still allow suffering a few minor bugs: The ultimate goal of Six Sigma is to achieve perfection. However, removing absolutely every error is not real. It is important to determine the level of error acceptable and focus on minimizing the errors have the greatest impact to customers.
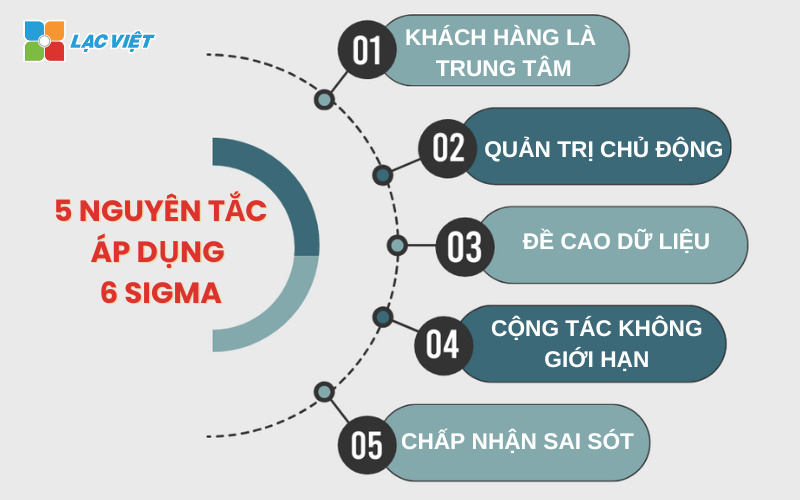
3. How to apply Six Sigma to process operated DMAIC
DMAIC is a process to operate the most basic is widely used in Six Sigma that most of the business application. This process includes 5 steps:
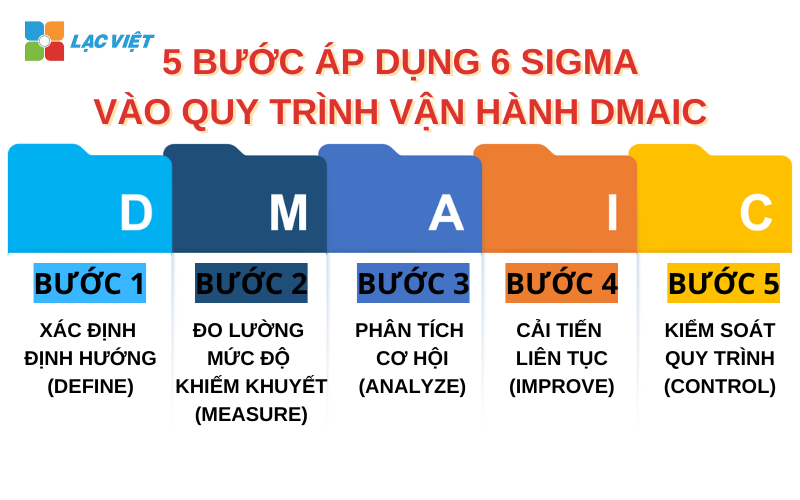
Step 1: Determine the orientation – Define
In the first step, businesses must clearly define the problem or need improvement, target customers and their requirements. Shaping clear goals will help for the next steps be performed in an effective manner, specific as follows:
- Identify the problem: What is happening is not right in the process? Problems that affect the customer like?
- Identify customers: Who are the people directly affected by this issue? What they need from the product or services of the us?
- Define goals: We want to achieve something after the completion of Six Sigma project?
Step 2: Measure the level of defect – Measure
In step measurement (Measure) will collect and analyze detailed data on the production process. The main objective is to determine the exact level of the current performance of the process and identify the weak points that need improvement. The main activity in phase Measure include:
- Collect data: Use the tools of statistical techniques to collect data in a systematic way, exactly. Data can include cycle time, error rate, production cost and quality indicators other.
- Performance reviews: Compare the index of the current performance with the objectives set out or industry standards.
- Determine the variables that influence: Identify the factors that can impact the outcome of the process, including the inputs, outputs,...
- Comparison with the standard Six Sigma: Đánh giá khoảng cách giữa hiệu suất hiện tại và mục tiêu 6 Sigma để xác định mức độ cải tiến cần thiết.
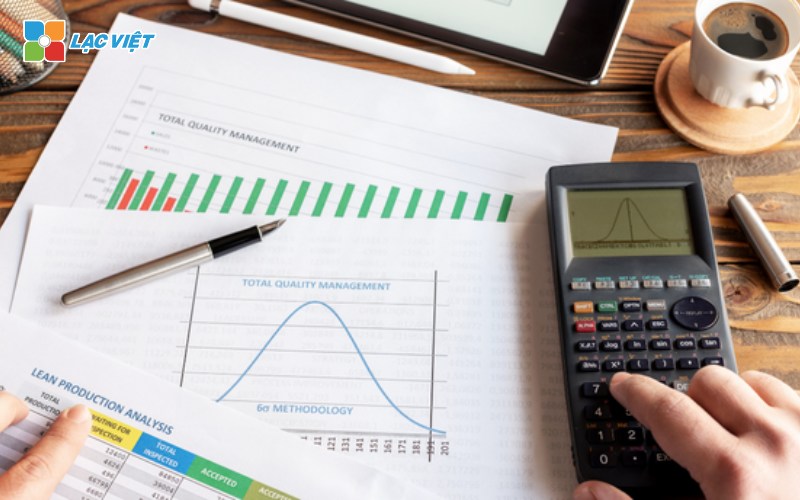
However, businesses are still stuck at the stage of measuring the level of defective because of the lack of baseline data for evaluation. When this software process management as LV-DX Dynamic Workflow will play the role tracking & progress monitoring, accurate real-time. Managers get any work finished/failure, causes of failure, the person responsible. Provides the data analysis, scientific reviews, to advance to the stage of continuous improvement.
Step 3: analysis of opportunities – Analyze
After the measurement cycle 6 Sigma in quality management will switch to analysis to determine the root cause causing problems or flaws in the production process.
Business will review the data collected in step measurement (Measure), aims to understand the nature, the distribution of them by the statistical tools. After that, the group of 6 sigma will determine the root cause through methods such as rule, Pareto charts, fishbone Ishikawa,...
Finally, summing up the results analyzed to draw conclusions about the main causes leading to the disparity between the actual process and quality standards, at the same time propose solutions for improvement. These results will be used to progress to the next step for improvement (Improve).
Step 4: continuous Improvement – Improve
At this stage, the group of six sigma will focus on the implementation of innovative solutions in order to minimize errors, improve the quality of products. The activities necessary to ensure the effectiveness and sustainability of process improvements including:
- Proposed improvement solutions: Based on the analysis results from step Analyze proposed solutions to bridge the gap between the existing process and quality standards set out. These solutions may be related to the change workflow, update technology, or systems new or staff training.
- Feasibility assessment: Conduct the experiment to test the feasibility and effectiveness of the proposed solution. At the same time check data as well as information to ensure accuracy, the practicality of the results.
- Implemented enhancements: After the solution is approved, the group Six Sigma will implement changes in the process. Make sure that these changes be made on time, scope and achieve improvement goals outlined.
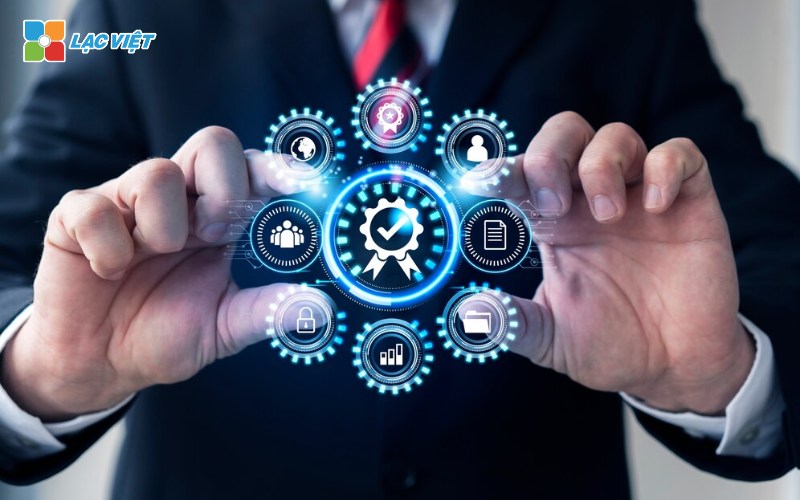
Step 5: process control – Control
Process control (Control) is the final stage in the process DMAIC of Six Sigma. Group on the implementation of 6 Sigma will establish control measures to ensure the stability and meet the quality target after implementation of the improvements. The main work includes:
- Building control system: Thiết lập các quy trình và cơ chế giám sát nhằm đảm bảo quy trình duy trì ổn định, đáp ứng các tiêu chuẩn chất lượng 6 Sigma.
- Set the monitoring indicators: The indicators identified in step Measurement (Measure) will be used to continuously monitor and evaluate the effectiveness of the process. Ensure that these indicators are monitored regularly to process operation standard.
- Set feedback system: Create feedback system quickly to detect to fix the timeliness problem occurs in the process, ensure stability in the future.
- Efficiency rating: Proceed to compare the indicators of quality, performance before and after implementation of improvements. This review will be done periodically to ensure that the process maintains stability meet the objectives set out.
4. Minimize error process operated with LV-DX Dynamic Workflow
LV-DX Dynamic Workflow is a technology solutions and business support optimize, automate business processes, from which minimize errors, and enhance transparency in all activities.
Some salient features of the LV-DX Dynamic Workflow:
- Digitizing the entire process onto a single platform: Provides a unified platform to digitize all the processes of the business, from hr, finance, accounting, business to production. Employees understand the roles according to the job titles do not COINCIDE work – making process.
- Task management excel with 3 not: No waiting – No clogging – don't forget to ensure the progress of the work is done on time, clear the wait state or jams work.
- Automate work-flow and delivery of the related departments: The work in process is automatically transferred to the next step upon completion of the previous stage, help to save time, minimize errors due to convey information.
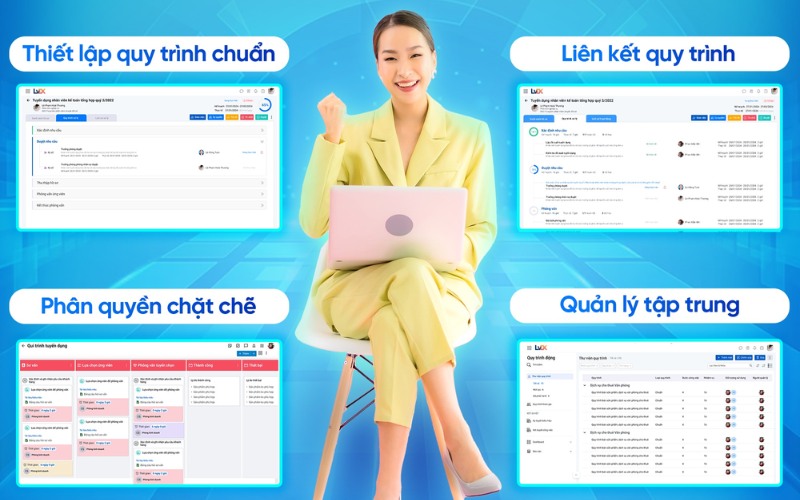
The article has to offer to you knowledge about 6 Sigma là gì as well as the principles apply it in business in the best way. Today, many businesses have and are applying this method to navigate to perfection in business. Hopefully with the useful information on can help you app six sigma a more effective way for your business.
CONTACT INFORMATION:
- Lac Viet Computing Corporation
- Hotline: 0901 555 063 | (+84.28) 3842 3333
- Email: info@lacviet.vn – Website: https://lacviet.vn
- Headquarters: 23 Nguyen Thi Huynh, P. 8, Q. Phu Nhuan, Ho Chi Minh city