In the business environment is increasingly competitive, quality products and services are important factors determining the success of the business. ISO 9001 – the international quality management system quality, not only help businesses improve quality, but also optimized the operation process, reduce risk, improve the satisfaction of customers.
However, many businesses still have difficulty in preparing resumes, selection, certification organization and optimize costs when implementing ISO 9001. This article Lac Viet Computing will guide details the steps required to businesses achieve ISO 9001 certification in an efficient way, quickly.
1. ISO 9001 what is?
ISO 9001 is the international standard on quality management (QMS), Organized by the international standardization (ISO) issued. This is one of the criteria that are applied most widely in the world, to help businesses establish, maintain, and improve management processes to ensure quality products and services consistently meet customer needs.
ISO 9001 does not give specific requirements about products or services that focus on business quality management, ensuring that products and services be produced provided according to the standard homogeneous, help increase reliability, improve operational performance.
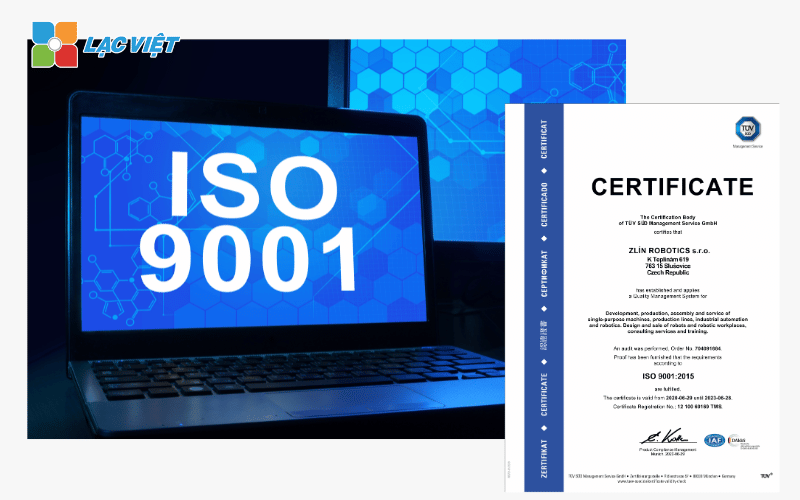
For example, a company manufacturing automotive components apply ISO 9001 to ensure each product has gone through verification process, strict quality control, avoiding the error production, guarantee safety for users.
2. The basic principles of ISO 9001
ISO 9001 is built based on the 7 principles of quality management to help businesses maintain stability in operations, continuous improvement to enhance efficiency.
2.1. To our customers
The core objective of ISO 9001 is to meet and exceed customer expectations. This is synonymous with the business need:
- Understand the needs, the wishes of the customer.
- Ensure products and services are high quality, reliable and stable.
- Continuous improvement to enhance customer experience.
For example, a company, ecommerce application of ISO 9001 will set the control process orders, to ensure products are delivered, right quality as committed.
2.2. The role of leadership
ISO 9001 emphasizes the importance of the leader board in the direction of the commitment system deployment quality management.
- Leaders must take responsibility to create environments that encourage innovation.
- Assigned the role of clear responsibilities in the organization.
- Ensure the necessary resources to implement and maintain ISO 9001.
For example, if a food manufacturing company to achieve ISO 9001 certification, leaders need to commit to provide adequate budget and personnel to build the system of quality control, staff training, performance evaluation, internal periodically.
2.3. Continuous improvement
There is no management system is perfect, right from the start, so the ISO 9001 requirements enterprises must constantly improved to enhance performance.
- Evaluate the effectiveness of the system of quality management periodically.
- Analyze customer feedback to adjust products and services more suitable.
- Remove the process is not effective, help businesses operate more flexible.
For example, a technology company applies ISO 9001 can improve the process of customer support by deploying chatbot AI to handle simple requests more quickly, reducing the load on the support staff.
2.4. Decisions based on data and evidence
ISO 9001 requires businesses to make decisions based on actual data instead of judgment feeling.
- Collects data on product quality, customer feedback, employee performance.
- Analyze data to detect errors and find the root cause.
- Based on the analysis results to adjust the process in a scientific way.
For example, a factory discovered the defective products rate spike in year 6. After analyzing production data, they realized the problem came from raw material in disqualification. Thanks to that, the business can quickly adjust the suppliers to ensure quality products.
2.5. Relationship management sustainable
ISO 9001 emphasizes the importance of building sustainable relationships with customers, partners and suppliers.
- Work closely with suppliers to ensure the quality of raw materials.
- Set long-term relationships with customers through after-sales service.
- Support training and development for employees to improve work productivity.
For example, a construction company applies ISO 9001 will work with the material supplier reputation, regularly check the quality of materials to ensure buildings meet the highest standard.
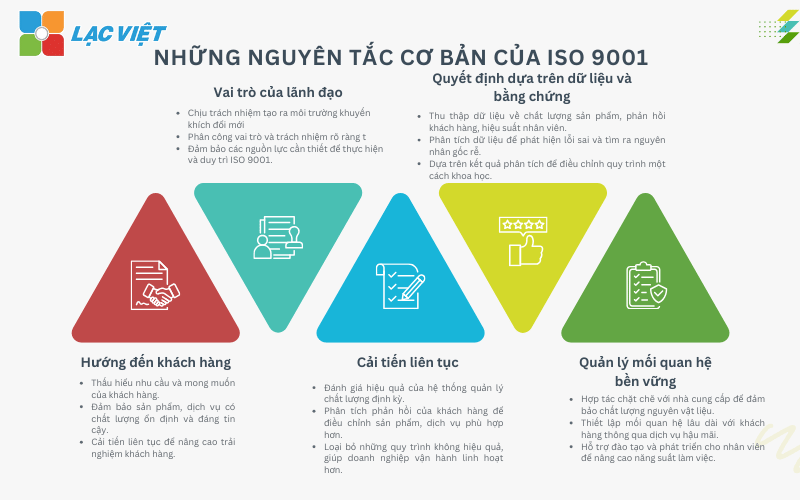
3. Benefits of ISO 9001 for business
ISO 9001 standard to help businesses comply with the regulations on the management of quality, improve operational efficiency, to enhance brand reputation. Below are the important benefits that the business will get when applying ISO 9001 in an effective way.
3.1. Improve the quality of products/services
Many businesses have difficulty in controlling product quality, leading to a manufacturing defect, products are not homogeneous or does not meet the requirements of customers.
Solution from ISO 9001
- Tightly controlled manufacturing processes, providing service: ISO 9001 requires businesses to set up system, quality management, in which all stages are to be monitored, strict control.
- Minimize errors, improve the uniformity of the product: The process is standardized to ensure all products/services are high quality, stable, limiting bugs.
Practical benefits
- Increase the rate of standard products right from the time the first production, reducing the number of defective products.
- Reduce the cost check back or withdraw the defective products.
- Raise the satisfaction of customers, retain loyal customers.
3.2. Enhance management efficiency, optimum operation
- Standardized workflow: Business need to establish the operating procedures standard (SOP) helps employees understand how to perform the job correctly efficiently.
- Remove the unnecessary steps: ISO 9001 help identify activities that do not create value, from which the optimization process to reduce wasted time and resources.
- Building monitoring systems, performance evaluation: The criteria for performance measurement (KPI) to help businesses monitor the level of completion of the work, the detection problem to improve.
Practical benefits
- Lose 20-30% of the time handle the job thanks to the process is standardized.
- Increase workforce performance when employees have clear instructions to avoid the overlap.
- Reduce errors in the process of commissioning, thereby reducing the cost to fix.
3.3. Increase brand reputation and ability to compete
ISO 9001 certification is evidence demonstrating the commitment of the business with the quality. This is an important factors help businesses enhance our position in the market.
Create trust with customers/partners: Customers tend to choose to trust the business has ISO certification because they believe that the product/services have stable quality.
Increased accessibility to the international market: Many multi-national companies require suppliers to have ISO 9001, this helps businesses easily expand business abroad.
Practical benefits
- Increase the rate of winning the project, big thanks to ISO 9001 certification.
- Attract more new customers thanks to the reputation in the market.
- Creating competitive advantage is clear when compared with rival not have ISO certification.
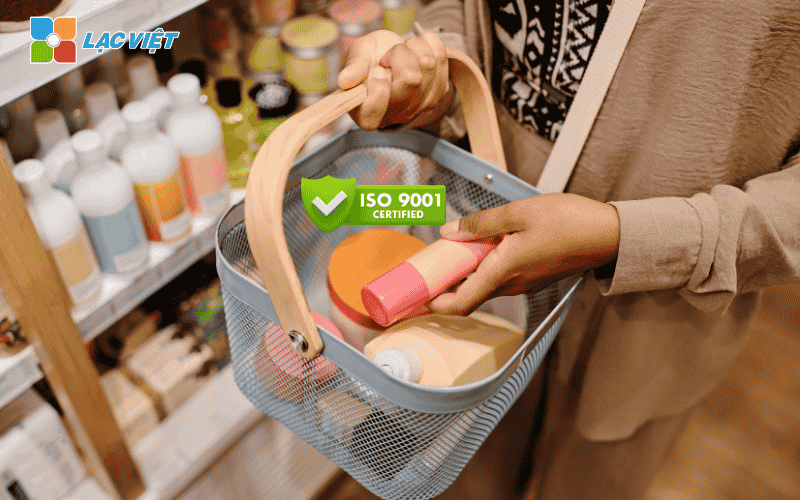
3.4. Cost reduction, operational risk
Build system to control quality strictly, all the flaws in the process are detected early and overcome before the product/service to the customer.
Process improvements to optimize cost: Thanks to the analysis of data quality, business can adjust the process to minimize waste.
Practical benefits
- Up 15-25% of production costs by reducing waste materials and stages of bug fixes.
- Minimize the customer complaints or returns due to product defect.
3.5. Raise the satisfaction of customers
- Build process customer care professional: Ensure all customer feedback is dealt with promptly and efficiently.
- Continuous quality improvement in products/services based on real feedback from customers.
Practical benefits
- Increase the percentage of customers who come back thanks to stable quality.
- Built files, customer loyalty, revenue growth sustainable.
4. The main requirements of ISO 9001
To implement ISO 9001 successful, businesses need to meet a number of core requirements to ensure system quality management, operational efficiency, continuous improvement and meet customer requirements. Here are the key requirements that businesses need to pay attention when applying this standard.
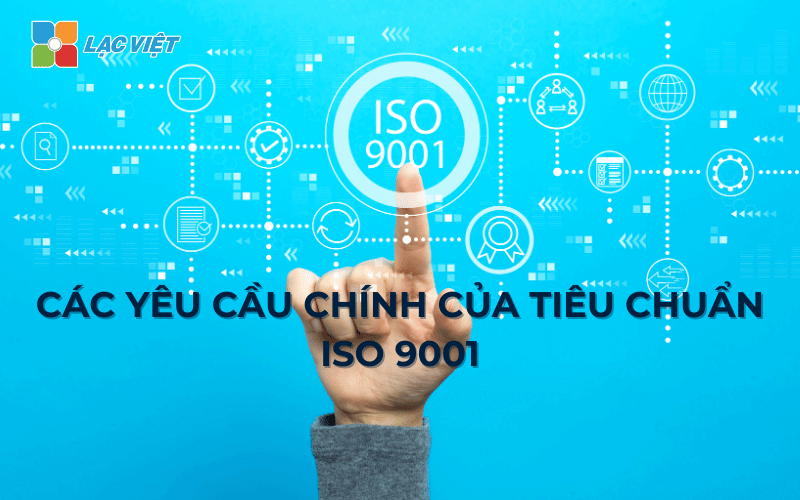
4.1. Policy and quality objectives
- Build quality policy clear: this policy should demonstrate the commitment of business with respect to the quality of product/service, satisfaction of customers, continuous improvement.
- Set goals specific, measurable: The objective quality must meet the principles of SMART (Specific – measurable – feasible – Related – for a limited time). For example: “Reduce the rate of defective products less than 2% within 6 months.”
4.2. Document control process
- Set system control of documents: All documents related to ISO 9001 (procedures, instructions, forms, reports) must be managed in a centralized version can clearly be updated periodically.
- Standardized workflow: build the operation procedures (SOP) to ensure all employees performing work under the guidance system....
4.3. The responsibility of leadership
Leaders need a clear commitment in implementing ISO 9001, expressed through the allocation of resources, time, create favorable conditions to parts made good system quality management.
Participate in the evaluation process improvements: leaders need to directly participate in meetings of quality review performance data, make decisions based on fact.
4.4. Opportunity assessment – risk
- Risk identification may occur: Business needs analysis of potential risks in the production process, operation, customer service and planning control.
- Take advantage of the opportunity to improve: in Addition to reducing risk, businesses also need to search for innovation opportunities, applied new technology or process improvements to enhance performance.
4.5. Staff training capacity
- Organize training courses on quality management system of: Employees need to understand how to perform the process, their role in the ISO system.
- Construction documentation details: Business need to have the visual material, easy to understand, so employees can refer to as needed.
- Training periodically updates new knowledge: ISO 9001 is the standard that need constant updates.
5. Guide to business development ISO 9001 success
Implementing ISO 9001 bring practical benefits, such as enhanced quality, optimized operation process, improve the satisfaction of customers. However, in order to implement successful business should have clear strategy, perform each step correctly and ensure the participation of the entire organization.
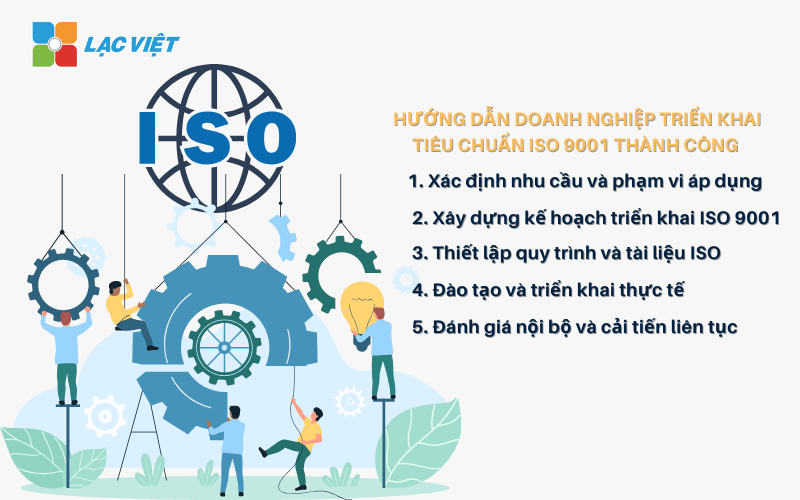
Here are detailed instructions to help businesses apply ISO 9001 effectiveness.
5.1. Identify needs/scope of application
Businesses need to decide if ISO 9001 will apply to the entire organization or only a specific department (e.g., production, quality control, customer service).
Identify the real needs of the business:
- Business application of ISO to improve processes, increase performance, or aim to achieve certification to expand the market?
- Any requests from customers or partners of the business to achieve ISO 9001 certification not?
For example, a company manufacturing electronic components can apply ISO 9001 for the production department to check the quality, then expand out to other parts such as logistics, customer care.
5.2. Construction plans to implement ISO 9001
No plans to deploy the tool can easily lead to the implementation of ISO discrete, lack of unity between the parts.
Need to establish a group in charge of ISO, this group will include representatives from the relevant departments, responsible for monitoring, implementing the requirements of ISO 9001.
Plan implementation in each stage:
- Phase 1: assess the current state identify where to improve.
- Phase 2: set process material according to ISO 9001.
- Phase 3: Training staff, testing new processes.
- Phase 4: internal Assessment and preparation for certification.
5.3. Set process/document ISO
Many businesses have processes that work are not clear, each department has ways to perform a private cause loss of quality control. ISO documents are not managed closely, leading to the situation that use of the material outdated or wrong process.
Hence the need,
- Write the ISO process, clear, transparent: Identify each step in the process, who is responsible for the implementation, the outputs desired what is.
- Document management ISO efficiency: Use the document management software to control the material version, ensure the employees are always using the latest information.
5.4. Training and implementation
Employees don't understand about ISO 9001, resulting in working condition according to the old habits, do not apply the new process.
- Need to organize training sessions practices: a guide workers on how to apply ISO on daily work. Training by real-life examples to help employees better understand the benefits of the system of quality management.
- Test deployment before widely applicable: Apply ISO 9001 for a small department in advance to check the effectiveness, then expanded to the entire business.
5.5. Internal evaluation and continuous improvement
Many businesses only focus on the achievement of ISO certification that do not implement continuous improvement then. Lack of internal evaluation, which makes the system ISO not exert the maximum effect. Hence the need,
Perform internal audits periodically: Check business can comply with the process have set no. Discovery point has not yet effective and give improvement measure.
Prepare for certification review ISO: Guarantee documents, the process is fully updated before formal assessment. Assessment organizations try to employees familiar with the process check out.
6. Businesses need to prepare anything to achieve ISO 9001 certification?
To achieve ISO 9001 certification, enterprises need to understand the standard, careful preparation of documentation, processes, as well as select institutions conformity assessment. The plan details to help businesses save time, optimize costs, guarantee certificate, effective practices, not indicative form.
Here are the important steps businesses need to be prepared to achieve ISO 9001 certification.
6.1. Record ISO documents should have
Enterprises need to build a system full documentation to prove that the system of quality management has been set up and are operating effectively. Here are the important documents required:
- Quality policy: Text demonstrating the commitment of the business of securing improve the quality of products/services.
- Standard working procedure (SOP – Standard Operating Procedure): guide details the steps to perform work in each department to help ensure consistency effect.
- Operating instructions, form control: supporting documents such as guide, quality inspection, handling process, when the problem and the form of the internal evaluation.
- Reports: internal evaluation: The results of the internal evaluation to be done before filing the certificate.
6.2. Select certification organization reputation
Select the organization is recognized by the competent authority, in Vietnam, the certification organization must be recognized by Ministry of Science and technology or organizations, international rating, such as UKAS, JAS-ANZ, ANAB.
Business can refer to the reviews from the company has been certified or check on the official website of the organization that issued the certificate.
Compare the cost and process assessment: A number of institutions have low-cost but quality inspection does not guarantee, while prestigious units usually have a review process post more.
6.3. Cost and time to achieve certification
Cost of certification depends on the scale of business:
- Small business (under 50 employees): the Cost ranges from 50 – 100 million.
- Medium business (50 – 200 employees): 100 – 200 million.
- Large business (over 200 employees): 200 million or more depending on the level of complexity.
The average time to achieve certification:
- The enterprise already has a management system, good quality: can be finished within 3 – 4 months.
- Business hasn management system basically: Duration can last from 6 months to 1 year.
The optimal way cost:
- Use management software ISO to reduce the time document management, staff training.
- Internal training instead of hiring outside experts to reduce the cost of advice.
The achievement of ISO 9001 certification not only helps businesses enhance credibility but also bring practical benefits such as improved performance, optimize processes and increase competitiveness in the market. However, to be successful, businesses need to prepare carefully profiles, selection, certification organization reputation, strategy deployment logical.
If your business is looking for solutions apply ISO 9001 effectiveness, let's get started today! Contact now Club Vietnam to receive a free consultation implement ISO system electronic.