Behind the impressive success from Toyota and Motorola are always the solution depth is to invest in research thoroughly. Let's find out how 2 big corporations this apply method Lean Six Sigma how to get results resounding like today. In this article Lac Viet Computing will analysis of the methods of Lean Six Sigma along the positive results achieved when applying.
1. Introduction to Lean Six Sigma
1.1 Workflow Definition
- Lean what is?
Lean is a management approach focused on optimizing processes, eliminate waste in the production process – service provider. By analyzing workflow, Lean help business remove the non-essential processes, increase efficiency. The goal of Lean is to achieve maximum value for our clients with the minimum waste
- What is Six Sigma?
Six Sigma is a method of quality management in order to minimize errors and fluctuations in the production process. Successful use measurement tools to improve the product, thereby increasing the satisfaction of their customers, and enhance operational efficiency.
- Lean Six Sigma combining like?
Is a combination of 2 methods of Lean and Six Sigma, aiming to achieve both achievements: process optimization as well as focus on quality. When combined, Lean Six Sigma to help businesses improve processes while improving product value – services.
1.2 history and development of Lean Six Sigma
- Origins of Lean
Lean originated from Toyota Production System (Toyota Production System), attention is paid to the optimization of the production stages by eliminating the unnecessary steps. This method became the foundation for the philosophy of Lean, help Toyota become the company the world's leading production efficiency.
- The advent of Six Sigma (Motorola)
Appearance in 1980 from the group Motorola, Six Sigma as a statistical tool and analysis to determine the root cause of the fluctuation. Six Sigma helped Motorola to achieve impressive results in the improvement of quality, at the same time contributing to this method became the standard in the industry.
- The combination of Lean and Six Sigma (The year 2000)
In the year 2000, notice the effect of 2 methods in this long time of apply. Lean and Sigma began to be combined together, creating a holistic approach to support improved operational processes. Many organizations after the application has received the results extremely aggressive in removing obstacles to stagnation in the production process, the service provider.
2. Basic principles of Lean Six Sigma
2.1 [5 principles] of the main Lean
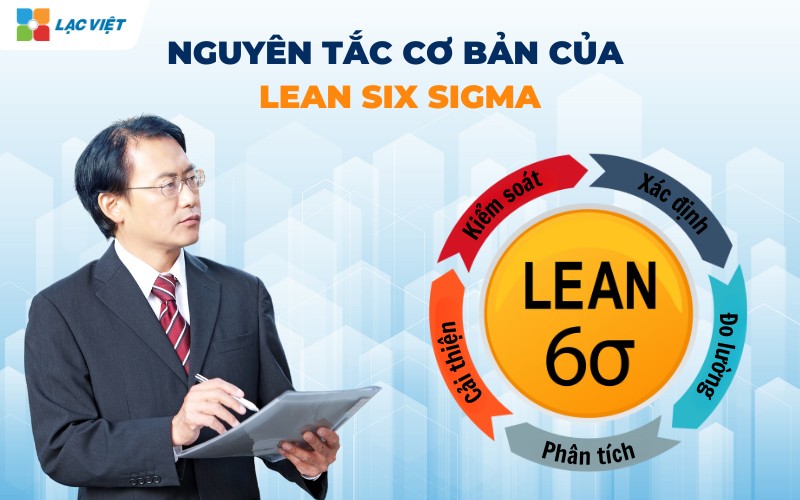
- Determine the value
Lean focuses on the capture and meet the customer's perspective. Businesses need to understand the needs and wishes of the guests to localize these factors create positive value. The operation does not create values, serving customer should be removed or improved accordingly.
- Mapping the value stream
This is step analysis process to determine the stage bring value to be useful and to eliminate unnecessary procedures. This step will give the angle overview for business about the machine operators to change strategy.
- Creating flow continuously
Build flow continuous operation will shorten the period of “dead”, enhanced efficiency and shortened resources wasted.
- Drag system
Drag system is the production method only when there is demand from customers, avoid mass-produced. This helps reduce the amount of inventory to ensure products are manufactured right time – the right quantity according to the requirements.
- Looking for the perfect
Focused on continuous improvement processes and products to achieve absolute perfection. Include the elimination of factors causing waste, improved quality of products, to meet the customer's expectations.
2.2 [5 stage] of Six Sigma (DMAIC)
- Stage 1. Define (Identify the problem)Focus : identify the issue backlog and navigation improvements after setting the project goals.
- Stage 2. Measure (Measure): Continuous data collection related to problems as well as measure current performance. Since then, business assess the level of errors, the rate of fluctuations in the process to provide information necessary for the analysis and improvement.
- Stage 3. Analyze (analysis): This phase focuses on analyzing data to help find the root cause of the problem. Determine the factors that need to improve, finding the right solution.
- Stage 4. Improve (Improve): Phase Improve will start deploying solutions to improve the process. Then, check the rating level of efficiency of the operation has tested to get results according to the initial target.
- Stage 5. Control (control): Last is to establish measures to control, maintain the improvement, support the process of continuous operation, has high stability.
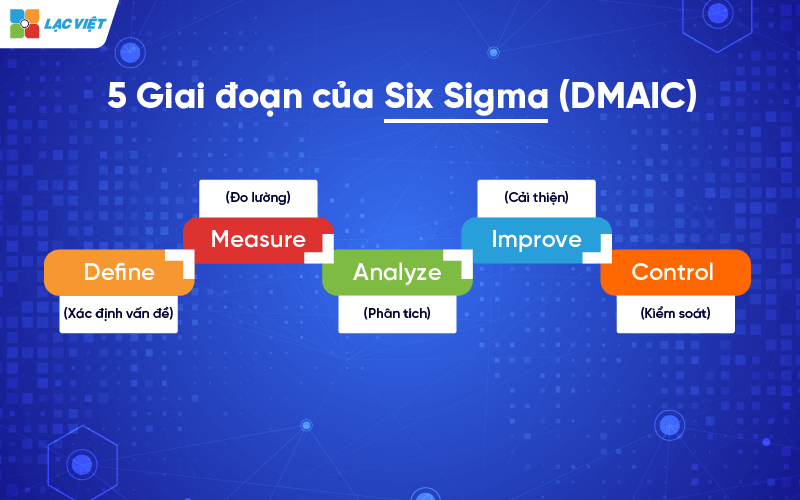
3. Why businesses should deploy Lean Six Sigma?
Business should deploy Lean Six Sigma for 4 following benefits:
- Enhanced performanceTo help businesses to use resources more efficiently thanks to optimized order of the operator. Eliminate significant waste unnecessary, improving processing speed and increased credibility for the brand.
- Improve the products and services: Minimize the errors, improving the quality of products before putting to consumers to increase the loyalty between the customer for the business.
- Enhancing competitiveness: Thanks to improved quality, responding quickly to the needs of customers. Business can increase its competitiveness in the market, maintaining its leading position.
- Building a culture of improvement: Benefit lies not only in the scope of business, Lean Six Sigma also building a culture of healthy business in the organization. Encourage employees to participate in process improvements and comments are constructive with the aim of product development.
4. Steps to implement Lean Six Sigma in business
To increase the level of efficiency for business when starting the application methods, Lean Six Sigma, be deployed in each step as follows:
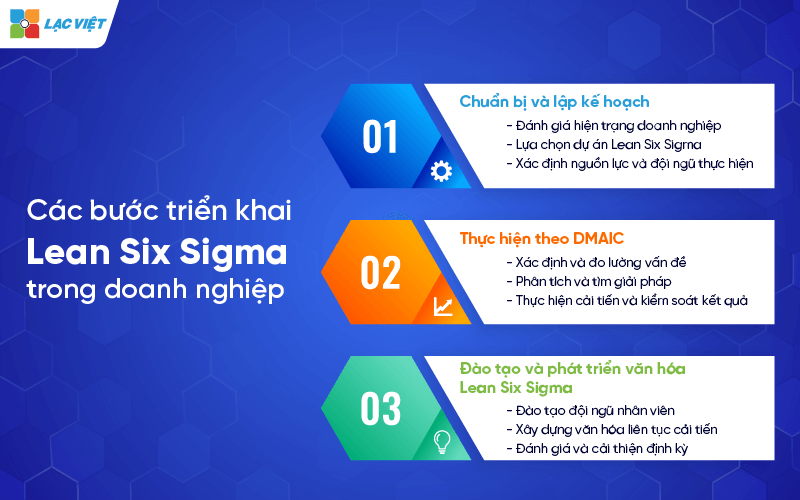
Step 1: planning
- Reviews the current state of business: analysis of current situation of the business, defining objectives that need improvement, and pondering the solution, may apply.
- Choose project: Select the project in accordance with the purpose business, ensuring the project has the ability to highest success.
- Determine the resources and team performance: planning and preparing resources to support the project, including: Resources; Costs; tools, project implementation, Lean Six Sigma.
Step 2: follow The DMAIC
- Identify the problem: Plan details the challenges, collect data, measure current performance to identify factors that need to solved.
- Analysis to find the solution: synthesis of the relevant statistics serve for the analysis of data, find the root cause of the problem helps businesses can put in place measures for improved fit.
- Improved implementation and controlling results: Start the implementation of measures to eliminate the shortcomings in the implementation process, constantly check the efficiency improvements to maintain.
Step 3: Training and cultural development Lean Six Sigma
- Training staff: Provide the intensive training for staff about the deployment process, useful information related to Lean Six Sigma, committed to all employees understand to carry out.
- Building a culture of continuous improvement: promote the work environment positive, calling employees are required to participate in process improvement activities on spirit ready to meet when there are changes.
- Reviews improved periodically: perform periodic reviews, check the performance and orientation for next improvements.
5. Case Studies – Success of Lean Six Sigma in practice
Toyota
Toyota Motor Corporation is the manufacturer of leading automotive world in the early 2000s. Before that, Toyota noticed the problem waste in the stage production of the car by the backlog of raw materials, time, “death” lasts. To solve radical, Toyota determination to apply Lean principles and use pull system (Pull System) has achieved success as today.
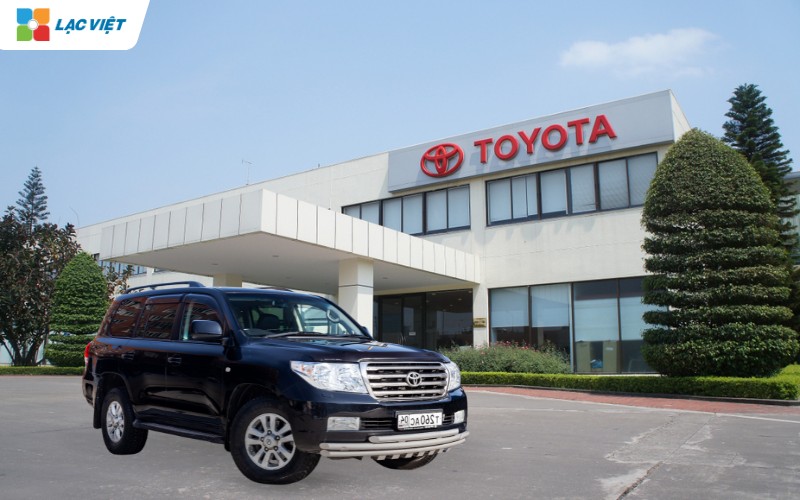
Results achieved:
- Shorten duration: Waiting time in the production process reduced from 25% down to 10% to help increase the speed of completion. Source: Book “The Lean Thinking” by James P. Womack & Daniel T. Jones.
- Avoid waste: The company reduced the amount of inventory and unnecessary costs, while improving flexibility in production.
Motorola
Similar to the Toyota conglomerate, Motorola came from America, famous for industry, telecommunications equipment, electronic, also faced with the problem of the defective products rate is high, the quality is uneven. Motorola successfully applied methods of Six Sigma with tools DMAIC to improve the production process and bring visible results.
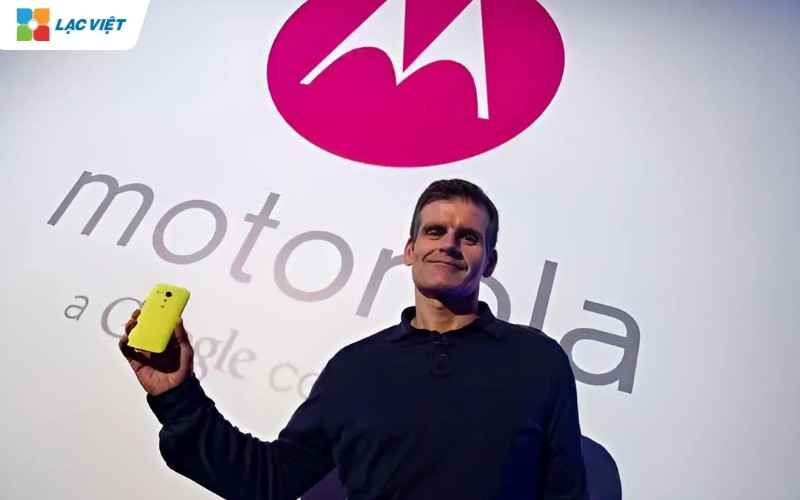
Results achieved:
- Reduce the error rate: Motorola reduce the amount of processing issues, defective products from 25-40% (cost of revenue) down to 5%.
- Increase evenly for products: After improvement, the plant was brought to the product have uniformity and quality.
Can say, Lean Six Sigma method is useful to business on the road to product development, enhance the level of customer satisfaction. Although, this method requires thorough preparation, the level of consensus between leaders with employees, but the effect that it brings extremely worthy.
CONTACT INFORMATION:
- Lac Viet Computing Corporation
- Hotline: 0901 555 063 | (+84.28) 3842 3333
- Email: info@lacviet.vn – Website: https://lacviet.vn
- Headquarters: 23 Nguyen Thi Huynh, P. 8, Q. Phu Nhuan, Ho Chi Minh city