The application of ISO process, not just a compliance requirement but also a strategy to help businesses optimize operations, improve performance and ensure quality products and services. However, many businesses have difficulty in the process of implementing ISO do not have a clear way to build, manage, and maintain processes in an effective way.
So ISO process what is, why businesses need to apply and how to deploy successfully? This article Lac Viet Computing will provide detailed instructions to help businesses achieve ISO certification, as well as utilize ISO to create competitive advantage and sustainable.
1. Process what is ISO?
ISO process is the set of steps taken in a systematic manner to ensure business compliance with the ISO correctly, efficiently. This is method to help businesses establish, maintain and improve the management system according to international standard.
In a business, every parts are the processes operate separately, but without the strict control of this process can lack consistency, which leads to errors, wasted resources, affect the quality of products or services.
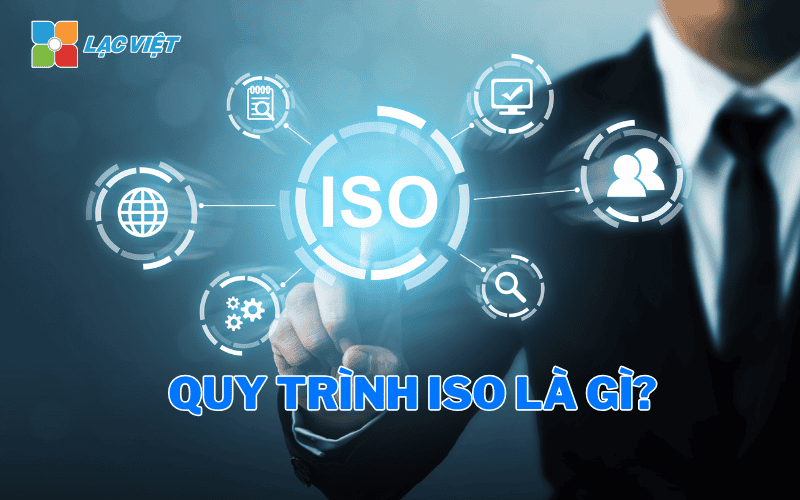
ISO helps enterprises standardize processes, ensure:
- Consistency: All activities are performed according to a standard procedure, avoid the difference between the parts.
- Higher efficiency: Reduce errors due to human limitations duplicate work and optimal execution time.
- Easy monitoring and improvements: Thanks to the clear standards, businesses can monitor performance, adjust promptly when problems arise.
For example, a manufacturing business apply ISO 9001 – quality management Systems quality will have process inspection raw material input, production, product inspection before leaving the factory. If there is no ISO, each production will likely follow different ways, causing difficulties in quality control.
2. Why enterprises should build process ISO?
2.1. Ensure the quality of products and services according to international standards
One of the biggest benefits of the ISO process is to help the business ensure the quality of products and services according to international standards.
- ISO provides detailed instructions on how to perform the work to achieve the highest efficiency.
- Help business control each stage of the production process or service delivery, from raw material input to products output.
- Ensure the product or service is consistent, synchronized, to avoid this shipment to another shipment to another.
For example, in the food industry, if the business application of ISO 22000 – management System, food safety, they have to control the entire supply chain to ensure food is not contaminated or infected with harmful chemicals.
2.2. Improve the efficiency of internal management, reduce risk in the operation
When businesses do not have clear process, employees can perform the work in its own way, leads to the overlap, lack of consistency, easy-to-happen errors.
Benefits when applied ISO process:
- Standardized way of working: Employees specific instructions on how to perform each task, to minimize ambiguity to avoid errors should not be.
- The ISO standards help businesses identify risks in each process, giving control measures early. For example, ISO 45001 – System safety management and occupational health to help businesses minimize the risk of occupational accidents.
- Optimized workflow: remove the unnecessary step, reducing the time taken to optimize the resources.
For example, a business in the logistics field application of ISO 9001 will have a clear process for check orders, packing, shipping. Thanks to that, they minimize errors in delivery, enhanced customer experience.
2.3. Create competitive advantage, meet the requirements of the partner/customer
In the business environment today, many customers and partners require businesses to have the certification of ISO new sufficient conditions of cooperation.
ISO help business:
- Create trust with customers/partners: A business achieve ISO certification to prove they have the management system, good quality, works according to international standards.
- Expand business opportunities: Many large companies, especially multinational corporations, only partner with suppliers who are ISO certified.
- Enhance brand reputation: When have ISO, business easily promote the image of professional, reliable on the market.
For example, a manufacturing enterprise electronic components are certified to ISO 9001 will be easily accessible to the customer such as Samsung, Apple more than businesses do not have certification.
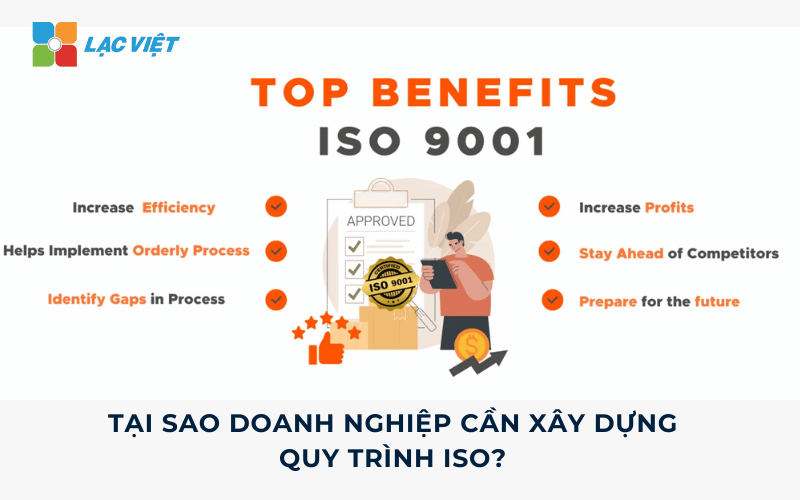
3. Deployment process the ISO downloads
The selection of ISO fits depends on the area of activity and the needs of the business. Here are four standards of ISO, most popular, instructions on how enterprises can deploy them in an effective way.
3.1. ISO 9001 – management process quality
ISO 9001 is the most common standard on quality management (QMS), to help the business set up process to make sure products and services meet customer's requirements, the relevant provisions.
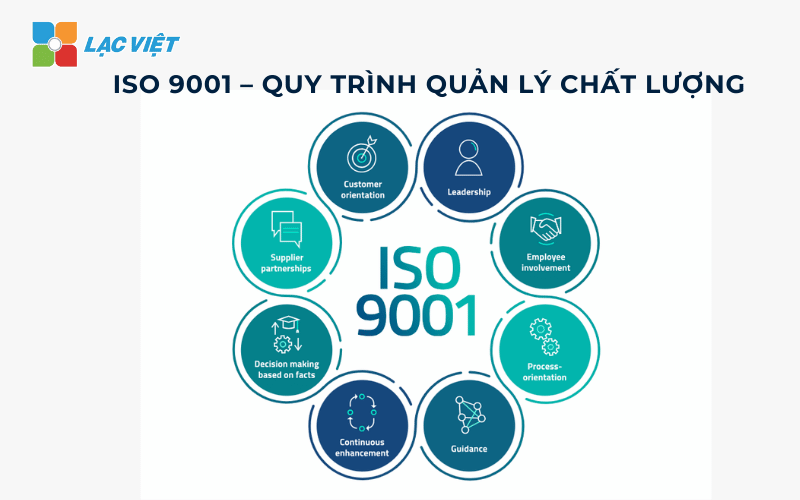
Instructions on how build process ISO 9001 for business
- Step 1: Determine the scope of application of ISO 9001: Businesses need to define the scope of application of ISO 9001 for the entire organization or only a specific department (e.g., production, quality control, customer service).
- Step 2: construction management documentation quality: including the quality manual, operation procedures (SOP), work instructions, forms control.
- Step 3: deploy the training of personnel: Employees should be trained on how to perform the process according to ISO 9001 standard to ensure consistent and effective.
- Step 4: Check out, internal evaluation and improvement: Business performing internal reviews to identify weaknesses, then continuous improvement to optimize performance.
How to document control and quality improvement according to ISO 9001
- Document control: document storage on digitizing system to easily access, update.
- Quality improvement: regularly collect feedback from customers, analyze the cause of the error, take out the remedies.
3.2. ISO 14001 – process management-environmental
ISO 14001 helps businesses build systems environmental management and minimize negative impact on the environment in the process of operation.
The step implementation process of ISO 14001 in order to reduce the environmental impact
- Step 1: assess the impact on the environment: determination of the activity of the business that affect the environment, such as air emissions, water emissions, solid waste.
- Step 2: build the control plan environment: the set up process waste, optimize energy use, reduce consumption of resources.
- Step 3: implementation, monitoring: Put into practice the policy of environmental protection, tracking, measurement indicators related.
- Step 4: enhancements and report compliance: building reporting system environment, ensure compliance with legal regulations, continuous improvement.
Integrated guide, the process environment to production activities, business
- Apply green technologies in the production process.
- Guide staff to carry out the operation environment-friendly.
- Set early warning system when there are environmental risks..
3.3. ISO 27001 – process safety management information
ISO 27001 is the international standard of management system for information security (ISMS), to help businesses protect important data from the risk of theft, leakage or loss.
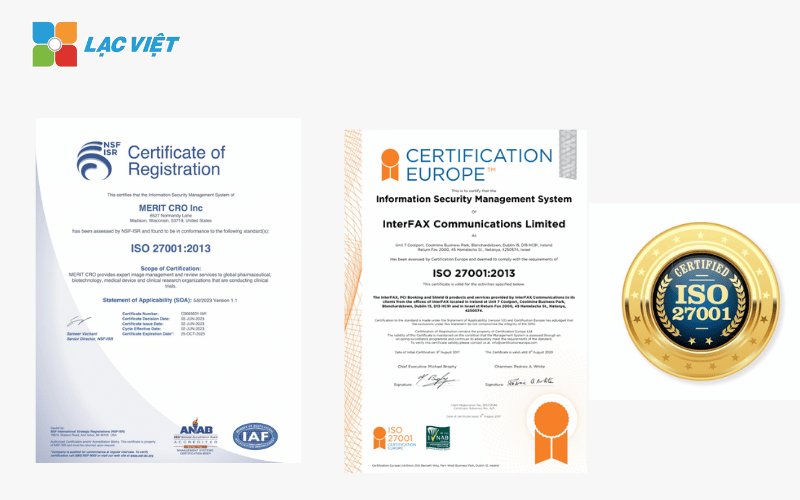
Steps to implement ISO 27001 in order to protect business data
- Step 1: assess security risks: Identify sensitive data of the business and the threat potential (network attacks, unauthorized access, data loss).
- Step 2: build privacy policy: set the process control, access, data encryption, user authentication.
- Step 3: staff Training on information security: a guide workers on how to protect sensitive information, detects acts of intrusion unusual.
- Step 4: Check and continuous monitoring: Applied technology, monitoring system, perform security checks periodically updates preventive measures against risks.
How to monitor, control, information security standards ISO
- Control access: The right to delete so that only the authorized person can access the important data.
- Backup data recovery: to establish a mechanism to backup data periodically in case of network attacks.
- Security report: construction process, report incidents, respond quickly when there is breach of security.
3.4. ISO 45001 – process safety management, occupational health
ISO 45001 helps businesses ensure safety for workers by controlling risks in the workplace.
Guide to building business processes ISO 45001 to ensure labor safety
Step 1: Identify safety risks, labour: Review of potential risks such as occupational accidents, exposure to toxic chemicals, risk of fire and explosion.
Step 2: construction safety policy and staff training
- Build process work safe, fully equipped with means of protection of labor.
- Organize regular training on skills troubleshooting, first aid.
Step 3: Check monitoring working conditions: periodic inspection of equipment, work environment, to detect risk, take corrective measures in a timely manner.
How to identify risks, take out preventive measures in the ISO system
- Periodic review: inspection institution of occupational safety frequently to detect risks.
- Early warning: set warning system when the problem occurred.
- Continuous improvement: the proposed measures for improvement of working conditions based on feedback from staff.
4. The step by step build deployment process ISO in business
The construction of implementing ISO process requires a systematic approach to ensure the effectiveness, in accordance with the actual operation of the business. Here are the important steps to help businesses apply ISO process in a successful manner.
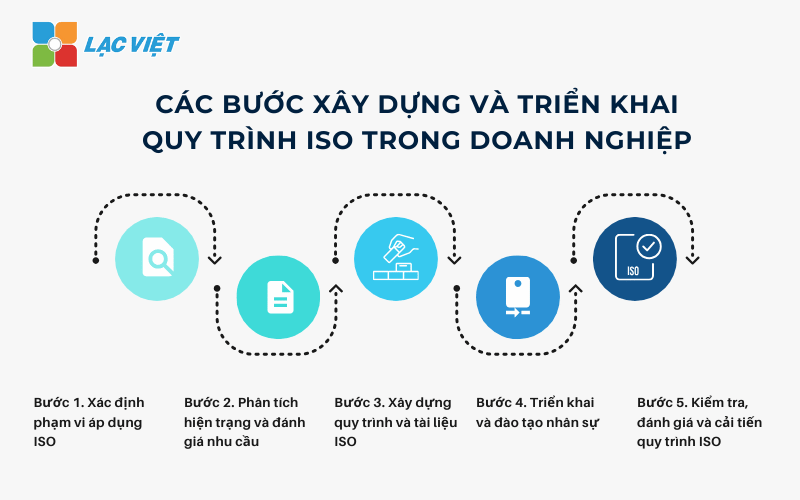
Step 1. Determine the scope of application of ISO
Some businesses when implementing ISO does not clearly define the scope of application, leading to the deployment status, spreading, no focus or overloaded resources.
Solution:
Identify areas should apply: Business need to decide on the ISO will be applied to the entire organization or only a specific department (e.g., production, quality management, customer service).
Determine the ISO in accordance with the field of operation:
- Business production → ISO 9001 (quality), ISO 14001 (environment), ISO 45001 (occupational safety).
- Business technology → ISO 27001 (information security), ISO 20000 (IT service management).
- Food business → ISO 22000 (food safety).
Determine the business benefits the desire to achieve: Reduce errors in production, improve the quality of service, meet customer requirements or improve performance?
Step 2. Situation analysis, needs assessment
No less enterprise deployment of ISO, but do not judge the mood before, leading to difficulties in tuning the old process to match ISO standard.
Solution:
Assessment management system current:
- Workflow is that it might meet the requirements of ISO not?
- The weaknesses in the management of quality, safety, information, or control the environment?
Planning to switch from the old system to the ISO system:
- Determine what changes need to be made to meet the ISO standard.
- Expected cost, time and personnel needed to implement ISO.
Step 3. Construction processes and materials ISO
Many businesses do not have the document clear process, leading to the deployment of ISO to the lack of consistency, hard to control.
Solution:
How to write process ISO standard according to the requirements of each standard:
- Step by step description perform the work according to the ISO standard.
- Clearly define the responsibilities of each department in the compliance process.
Documents required in a system, ISO post:
- Quality manual: a Summary of policy and quality objectives of the business.
- Standard working procedure (SOPs): detailed guide step by step perform the work.
- Operating instructions: detailed documentation on how to use the system equipment.
- Form control: document Template to monitor the implementation process of ISO.
Step 4. Development and training of personnel
Staff not familiar with the system ISO new lead to improper execution of the process or resistance to the change.
Solution:
Guide staff on how to implement ISO process in daily work:
- Clearly explain why business apply ISO and the benefits they will receive.
- Provide documentation easy to understand, so employees can refer to as needed.
Organize internal training to raise awareness about ISO:
- Training in the form of practice rather than theory alone.
- Use real world situations to help employees understand, apply on the job.
Step 5. Test, evaluate, process improvement, ISO
After applying ISO, many businesses do not perform periodic reviews, lead to system ISO gradually become form, do not bring the actual efficiency.
Solution:
How businesses make internal evaluation and process improvement continuous:
- Perform periodic reviews to check the level of compliance.
- Identify the points not yet effective suggestions for improvement.
Integrated technology to optimize process control comply with ISO:
- Application management software ISO to automate document control, tracking process.
- Use early warning systems to detect, remedy the problem promptly.
5. The important note when implementing ISO process
The application of ISO process to help businesses standardize operations, enhance performance, ensure compliance with international standards. However, if not properly implemented, the business can meet many obstacles that prevent the application of ISO becomes difficult, less effective. Here are the important note to ensure the process of implementing ISO smoothly and achieve the desired results.
5.1. Avoid these common mistakes when applying ISO process
Error 1: document Management, asynchronous
One of the greatest difficulties when implementing ISO is the document management do not sync between the parts. When the business is still using paper or Excel file to store documents ISO status, use version document outdated or no control of the content may occur.
Solution:
- Building management system documentation focus, where all procedures, instructions and forms are updated, version control.
- Specify a department responsible for document control ISO to ensure the accuracy consistency.
Error 2: No control good compliance between the parts
Many businesses have difficulty in ensuring that all parts are properly implemented ISO process. If some parts adhere tightly while the other parts not done correctly, the ISO will not bring efficiency synchronous.
Solution:
- Set up system monitoring, periodic reviews to ensure compliance.
- Provide clear instructions, training employees in all parts.
- Build feedback mechanisms so employees can report if there are difficulties in the implementation process of ISO.
Error 3: Lack of employee engagement and leadership in the deployment process
Some businesses only focus on the quality management department or a small group in charge of ISO, while the other staff does not really understand or not trained on the process ISO. This leads to implementing ISO becomes form, do not go into reality.
Solution:
- Leaders need to show clear commitment by participating in meetings, reviews, and support resources to deploy ISO.
- Training employees on the content of ISO, the benefits that they get when adhere to this process.
- Create environment that encourages employees to contribute ideas to improve the process ISO.
5.2. Software use ISO-electronic to optimize process management
When applying ISO according to time, track progress, update documentation, compliance monitoring, evaluation reports often take a lot of time. Input errors or forget to update the information can affect the effective implementation of ISO.
Solution:
- Digitization process ISO: Using software to automate document storage, tracking process and send alerts when there are changes.
- System integration progress tracking: The software can display the KPI on the level of compliance, the progress of the internal evaluation, the points to improve.
- Automatic reports: Instead of collecting data, the system can automatically aggregated reporting for businesses to have a holistic view of compliance status ISO.
5.3. Combined control ISO with the other management system
Many businesses deploy ISO separately, not integrated with the other management system as ERP (system resource planning enterprise) or CRM (system management customer relationship). This led to the division operation, discrete, lack of connection information, difficult to optimize operation.
Solution:
- Integrated ISO with software, ERP, CRM: this helps businesses manage information related to ISO (such as production processes, quality assessment, customer feedback) automatically, synchronized with system manager general.
- Leveraging data ISO to enhance the performance work: Instead of just see ISO is a standards compliant, businesses can analyze data from the ISO system to improve performance, optimize production processes, improve the customer experience.
- System setup smart alert: When there are deviations in the process, or risk incurred, the system can automatically send an alert to the relevant department for immediate processing.
Deployment ISO process not only to help businesses comply with international standards, but also contribute to improving product quality, optimizing operation and enhanced reputation in the market. However, to achieve maximum efficiency, businesses need to plan to deploy basically, avoid the common error, and ensure the participation of the entire staff, leveraging technology to optimize management ISO. If your business is looking for a method of implementing ISO electronic efficiency. Contact now to get free consultation and documentation, detailed instructions on the process ISO!